Before (改善前)
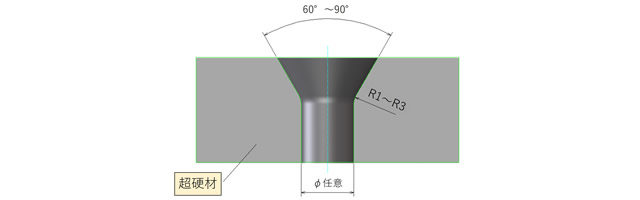
放電加工は加工形状に合わせて工具電極を成形する必要があります。そのため、複雑な形状になればなるほど電極の成形に工数がかかってしまいます。例えば、上図のように超硬合金を用いて片方からはストレートな仕上げ孔加工、もう片方からテーパ角度60°~90°のテーパ加工、更につなぎ目にR1~3を持たせたような形状の場合、放電加工で使用する電極も複雑形状となり工具電極成形のリードタイムが伸びコストアップしてしまいます。
V
After (改善後)
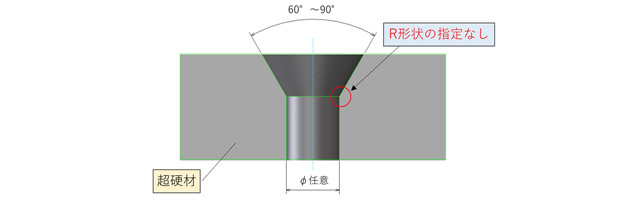
工具電極の形状を単純化することで、放電加工時のコストを抑えることができます。従来設計では孔加工とテーパ加工のつなぎ目のRをR1.0~R3.0で指定しました。しかし、仕様上問題がない場合はつなぎ目部分のR形状を任意に変更することで、つなぎ目を放電加工ではなく「リューター」と呼ばれる工具を使用し加工することが可能になります。R部の放電加工を行わなくて済むため、電極の成形時間を抑えることができ、コストダウンを実現することができます。